Black Oxide Drill Bits are made by heating HSS bits to at least 950 degrees Fahrenheit. The process produces a black oxide finish that has corrosion resistance and is rust-resistant. They are the most commonly used drill bits in the industry.
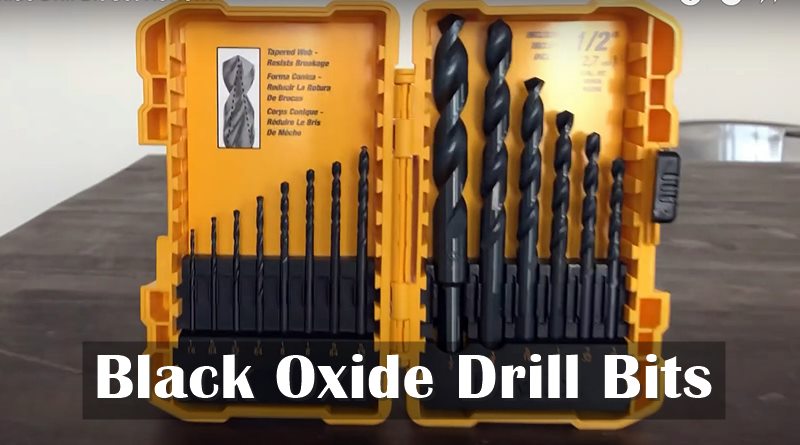
Black oxide is one of the most aggressive tungsten carbide grades, with a hardness rating that exceeds any other grade by 20 points. This means that they are incredibly durable and can be used to cut through more complex materials than any other type of drill bit.
This article gives a deeper analysis of oxide drill bits, the types, how to use them correctly, and some maintenance tips to increase longevity.
Table of Contents
What are Black Oxide Drill Bits Used For?
There are several black oxide drill bits, each with diverse usage. The most popular ones are twist drills that drilling holes in steel and cast iron materials. X-cutter style drill bits are often seen on construction sites when deck construction, fences, and other usage areas. Black oxide drills work best on softer wooden materials.
The black oxide drill bits are the strongest and can be used for multiple applications, such as drilling holes in brick, concrete, or stone materials. They are also suitable for steel, aluminum, copper, brass, oak, maple, pine, PVC, MDF, acrylic, ABS, nylon, among other composite materials.
Black oxide drills should never be left to sit for too long without use because the protective coating will wear down. Therefore, proper storage is an essential maintenance option for black oxide drills.
Black Oxides vs Titanium Drill Bits:
Black Oxide Drill Bits come with a protective coating for a finish but are not shown on Titanium Drills.
Black Oxide Drill Bit’s hardness rating exceeds any other grade by 20 points, making it highly durable while drilling through harder materials. In contrast, Titanium has difficulty penetrating when dealing with much tougher materials such as hardwoods, concrete, or steel.
Titanium coating on bits can be used to bore holes up to 6000 feet deep due to its ability to cut tungsten carbide unlike other types of drill bits.
Black Oxides’ coating wears down and needs to be replaced when the drill bit is not used, whereas Titanium nitride does not require this maintenance.
How to Use Black Oxide Drill Bits
The black oxide drill bit and cobalt bits needs you to exert pressure and then rotate them slowly clockwise. through the drilling process.
Apply a slight downward force on your black oxide drills or cobalt bits while rotating for maximum torque and drilling efficiency.
We recommend applying a good quality cutting oil before usage for the black oxide drill bit’s longevity. This will enhance the drill’s lubrication and that they remain sharp while drilling through any surface hardness.
For best results, make sure they are well-sharpened before usage for easier penetration into more demanding materials. Sharpen these drills through abrasive paper or a grinding wheel. But don’t try filing with a metal file as it causes unnecessary wear and tear.
Can You Use Black Oxide Drill Bits For Wood?
Black oxide bits and cobalt bits are not the best choice for wood. The black oxide coating is very aggressive and can cause wear on softer materials such as wood, resulting in premature bit failure. If you need to use your black oxides drilling into rugged woods, we recommend using a Carbide-Tipped Drill Bit instead of a Black Oxide one.
Carbide tipped bit is more preferred in this case due to its ability to retain cutting edge hardiness when submitted to a high machining temperature. The carbide tips hold an improved surface finish with a longer size for higher quality at the end of the day.
We also recommend the carbide tipped bits for highly abrasive materials. However, black titanium oxide can be used for drilling through wooden materials, PVC, Fiberglas, and metal. The titanium bits have a long life span compared to lack oxide counterparts.
Winding up…
Black oxide drill bits are best for drilling harder materials such as steel, cast iron, or brick. It would be best to never use these types of drills on softer materials like wood since the black oxide coating can cause wear and tear resulting in premature bit failure.
Store the black oxide drills in a cool, dry place and have proper maintenance precautions, for instance, by applying adequate cutting oil and sharpening the bit for best black oxide finish.